Landeshauptstadt Dresden - www.dresden.de https://www.dresden.de/en/business/tomorrow-s-home/kuenstliche-intelligenz-eng.php 14.12.2023 13:39:33 Uhr 27.07.2024 08:14:49 Uhr |
|
Artificial intelligence in Dresden
Artificial intelligence is at home in Dresden
Be it search engines, smart cities or driverless cars, artificial intelligence (AI) is becoming increasingly prevalent even in everyday life. And the AI hub of Dresden is creating the perfect environment for this. The Saxon state capital is one of Europe’s leading high-tech locations, and is involved in further developing critical AI hardware, semiconductors and AI software. The high density of top-class companies, start-ups and research institutes based here makes Dresden a unique cluster for artificial intelligence.
Artificial intelligence up close and personal: The CeTI at TU Dresden
The ‘Centre for Tactile Internet with Human-in-the-Loop’ (CETI) wants its research to take co-operations between humans and machines to the next level. In the future, the aim is for humans to be able to interact in real time with networked systems in the real or virtual world. This will be made possible with the likes of smart sensor gloves, as developed by Dr Ievgenii Tsokalo from the CeTI in Dresden. The gloves can register even the tiniest of movements, and pass information in to the wearer via feedback. They are equipped with artificial intelligence to enable them to understand and process humans’ movements. This artificial intelligence is found directly on the gloves themselves (for the sensor processing) and in a nearby edge cloud. The edge cloud facilitates low latency periods and a high degree of reliability, both of which are important pre-requisites for real-time application. It is expected the technology will be used in medicine and industry in the future, such as for surgical robots or human-machine co-operations during assembly processes. CeTI’s aim is to democratise access to work-related expertise and skills in the same way the internet has democratised access to information.
Mimetik: Using AI gloves to reduce assembly-related stress
Mimetik is a spin-off of the TU Dresden’s ‘Centre for Tactile Internet with Human-in-the-Loop’ (CeTI), and was founded in early 2020 under the direction of Dr Ievgenii Tsokalo. Mimetik is working with the CeTI to further develop and launch a smart sensor glove to simplify manual work (see CeTI). To do this, the Dresden-based start-up has specialised in industrial applications of assembly technology. With an edge cloud and negative latency, the glove tracks its wearer’s hand movements in real time. Artificial intelligence then processes the movement data to support the user with intuitive feedback during the work process, or to help them learn new tasks. The glove can also alert its wearer to oversights, which can benefit assemblers, as they are susceptible to high levels of stress due to long phases of concentration. Mimetik currently employs 14 staff at its Dresden base.
Digital Production Factory 3: Improving the human-robot collaboration
Collaborative working between humans and robots could significantly increase efficiency in the production processes of the future. But there are still a few obstacles impeding industrial application of this technology – such as the risk of accidents and the issue of how service providers can best charge for their smart robots. These are two challenges that the Smart Systems Hub in Dresden is now seeking to tackle as part of its ‘Digital Product Factory’ innovation programme. Dresden chip manufacturer Infineon and software specialists SAP, objective partner and Wandelbots are all participating in the current programme to improve human-machine interactions. Together, the four companies are working to develop a smart production assistant.
The robot’s ‘eyes’ are being created by Infineon, while its ‘muscles’ are the responsibility of Wandelbots, and the ‘nervous system’ is the work of SAP and objective partner. What makes this project unique is the fact that, thanks to sensor fusion, artificial intelligence and the edge cloud, the robot is also able to recognise collaborative tasks and memorise certain work stages. In addition, the technology facilitates digital billing as a complete and scalable business model also known as ‘robot and asset as a service’. The Smart Systems Hub Dresden is designing the virtual and physical spaces for the co-operation, methodologically managing product development, and taking charge of organisation and acquisition of know-how.
Cloud & Heat: The world’s most energy-efficient data centres
Digital technologies are playing an increasingly important role in our lives, as has also been evidenced by the sharp rise in demand for high-performance IT infrastructure. This infrastructure consumes a tremendous amount of energy – a problem that Dresden-based IT company Cloud & Heat wants to change with innovative products and patented technologies. The aim is to build the world’s most energy-efficient IT infrastructures. And when it comes to hardware, Cloud & Heat offers its customers tailored data centres that use waste-heat technology and water-cooling to achieve the highest efficiency in their category, and which facilitate cost savings of up to 60 per cent. Coupled with this are AI-driven software solutions that optimise the capacity utilisation of local data centres and the overall grid. These are designed to enable synergies between data centres and the energy and heat market. The technology has great potential for saving energy and resources, and could play an important role in avoiding CO2 emissions in the future.
Bosch: Critical AI chops for the automotive industry
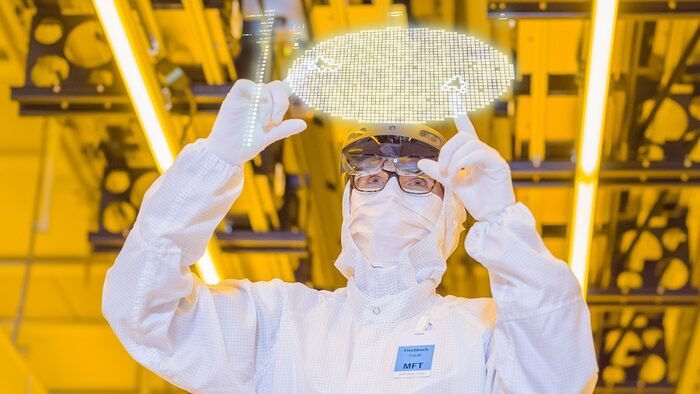
Bosch has invested some one billion euros in its Dresden ‘Waferfab’ – more than ever before in the company’s long history. The result? One of the world’s most state-of-the-art chip factories, producing 300-millimetre silicon wafers for the Internet of Things and future mobility. In doing so, Bosch is focusing on fully automated manufacturing with AIoT technology, i.e. a combination of artificial intelligence and the Internet of Things, laying the foundations for continuous, data-controlled improvement in production. For example, the tiniest errors (signatures) in wafer production can be detected by an AI algorithm, the causes analysed, and process discrepancies immediately corrected. In this way, the production process and quality of the semiconductors are constantly being improved, and the degree of process stability further increased. AI algorithms can also make accurate predictions as to whether and when a production machine or robot needs to be maintained or readjusted. This reduces not only the number of defects, but also the work so far needed to perform the maintenance. Production control is another area in which AI is used. Here, its computing and data power helps navigate the wafers through the up to 700 process stages in the approximately 100 systems at the factory in the most time and cost-effective way possible.
GLOBALFOUNDRIES: Neurochips and Edge AI
GLOBALFOUNDRIES has been producing at its Dresden base for 20 years. With now more than 3000 staff and a total investment of over 12 billion euros, the ‘Dresden Fab 1’ is Europe’s largest and most modern semiconductor factory. It is here that, in over 1000 work stages and with the support of Edge AI solutions, Globalfoundries builds state-of-the-art microchips for technology companies and car manufacturers all over the world. High-precision machinery is used to make the microchips on silicon wafers with structures up to 22 nanometres in size. With its special 22FDX technology enables Globalfoundries to build particularly energy-efficient circuits that can be used, among other purposes, to develop neural networks. Examples here include the international ‘Human Brain Project’, the ‘Zen’ concept and the ‘Spinnaker 2’ project run by the TU Dresden. Through its involvement in research and development, GLOBALFOUNDRIES has helped establish the semiconductor hub of Dresden as a leading centre for micro and nanoelectronics in Europe.
Fraunhofer IPMS: Neuromporphic Computing
Increasing digitalisation is raising the demands on electronic hardware. Speed, performance, miniaturisation and energy efficiency are becoming more important in order to enable applications in the areas of big data and artificial intelligence (AI). Neuromorphic computing offers a solution that aims to mimic the self-organising and self-learning nature of the brain. Fraunhofer IPMS is developing materials, technologies and complete hardware solutions with high energy efficiency for this purpose, particularly for applications in the edge area. For neuromorphic hardware, Fraunhofer IPMS is researching crossbar architectures based on non-volatile memories, the ferroelectric field-effect transistors. This is being done as part of various European (TEMPO, ANDANTE, STORAIGE) and Fraunhofer-internal projects (NeurOSmart). Particularly innovative materials research for future SNNs with Li-based systems is being conducted as part of the MEMION project in Saxony.